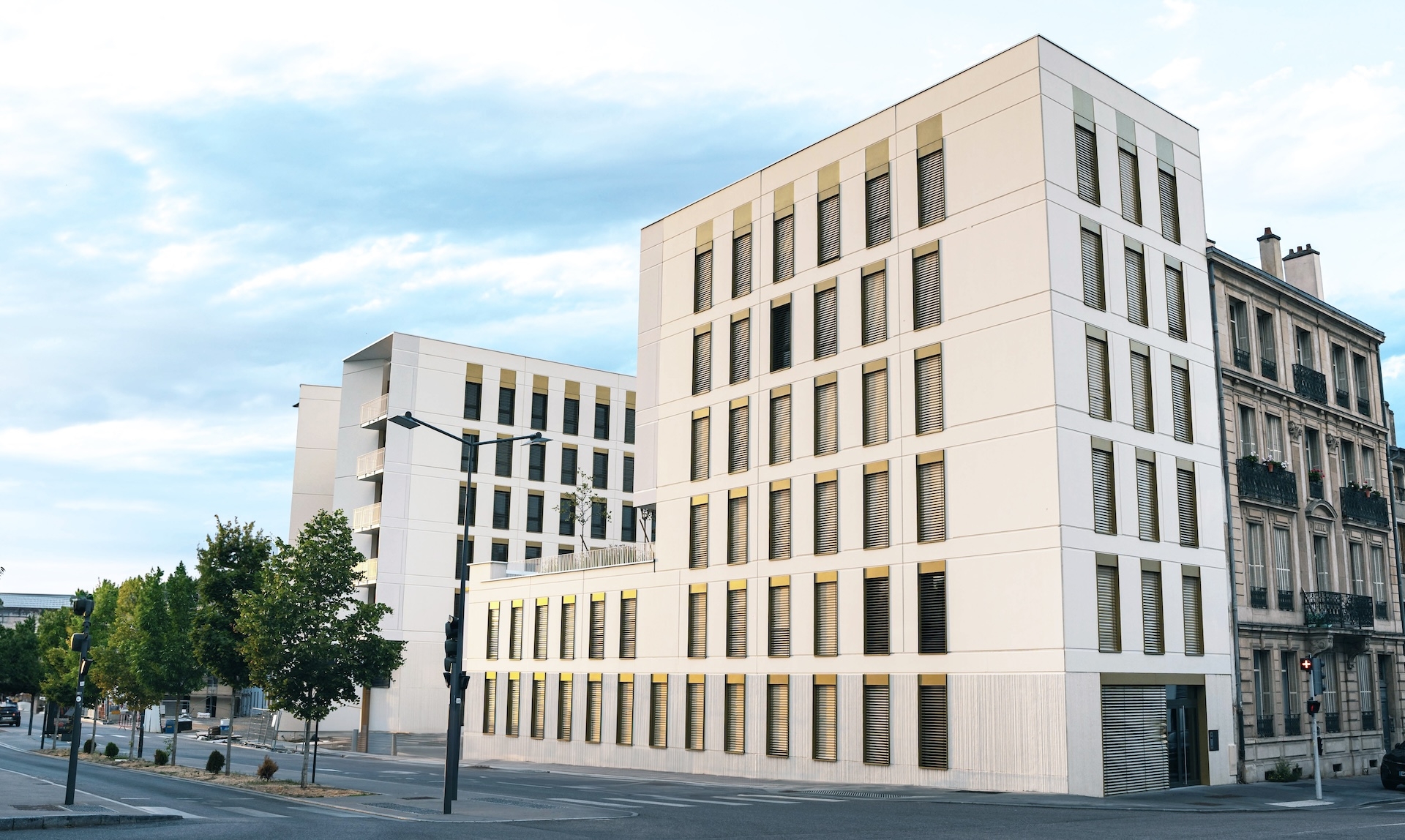
Our Environmental Commitment
The planet: the priority from which all others stem. At a time of major climate upheaval and unsustainable pressure on natural environments, protecting the environment through responsible construction is for us more than a 'simple' commitment: it's a given.
Our low-carbon solutionsBecause life is the basis of everything, FEHR Group makes no economic compromises on ecology and is already doing everything to build the world of tomorrow: the 'post-carbon' world. As an environmental player, FEHR Group places sustainable construction at the heart of its strategy.
- use of recycled aggregates and concretes with low environmental impact
- reduction of emissions and valorization of waste
- systematic preference for low-carbon materials
- production exclusively through internal material processes
- logistics via waterways and rail transport
- short supply chains and energy needs reduced to the bare minimum...
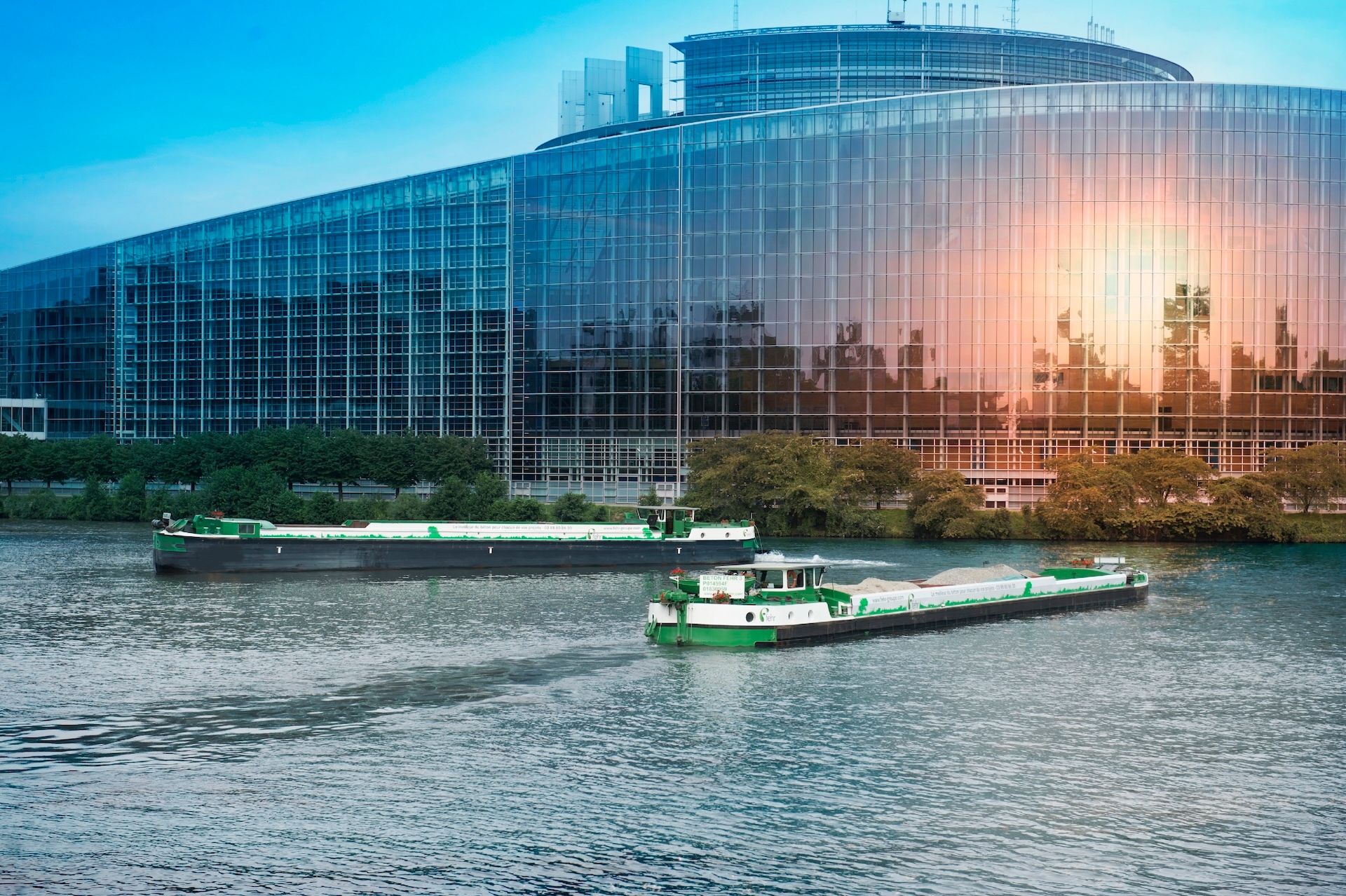
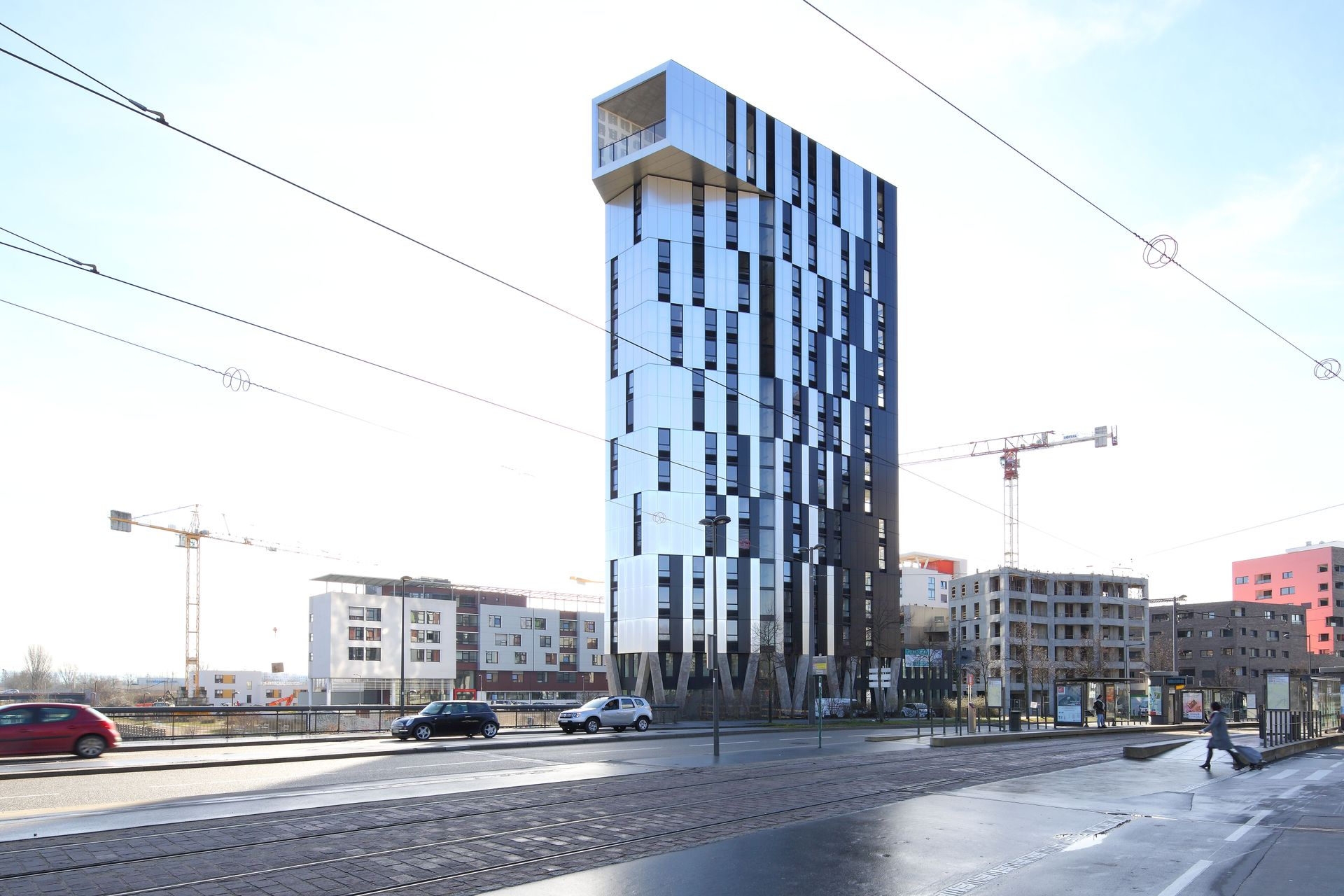
a long ecological history
A family business with strong values from Alsace, located for over fifty years at the border between France and Germany, FEHR has always been acutely aware of the environmental challenges of construction.
In this region, with largely intact natural heritage, FEHR was born from a dual desire: to offer durable constructions that do not trade reliability for environmental respect, and not to choose between performance and responsibility.
Today, more than ever, our company is happy to continue its primary commitment: to meet new ecological challenges while continuing its technological adventure. Fehr Group thus comprises 600 people, 10 plants, 4 production sites, and 1 state-of-the-art laboratory fully dedicated to research and production of increasingly clean, demanding, and functional concrete.
committed to efficiency
Since we are keen to prove that reducing the ecological footprint goes hand in hand with durable construction that is above all reliable, we explore all solutions to offer low-carbon and eco-responsible buildings.
In this context, we strive to use recycled aggregate as much as possible in the composition of concretes for which the only requirement is compression strength — the 'heavy concrete'. And we tirelessly mobilize our research unit to maximize the use of recycled concretes without any compromise on safety and the mechanical properties of the finished product.
Thus, we are engaged in a 360-degree environmental logic, which involves environmental management on our sites, in our products, and in our multimodal logistics.
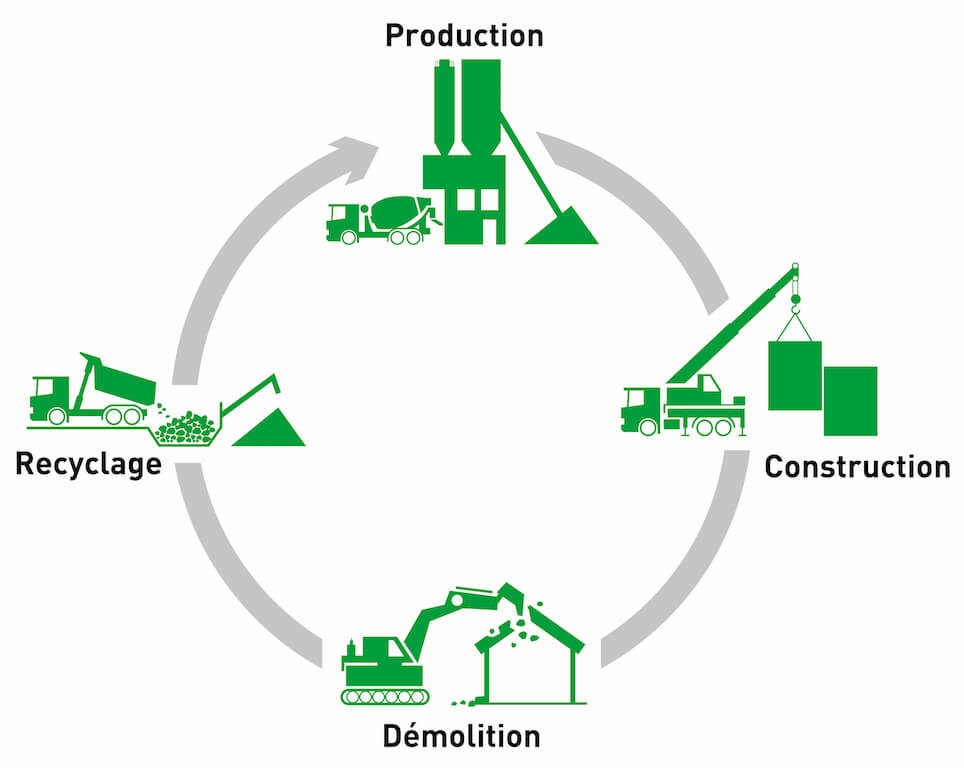
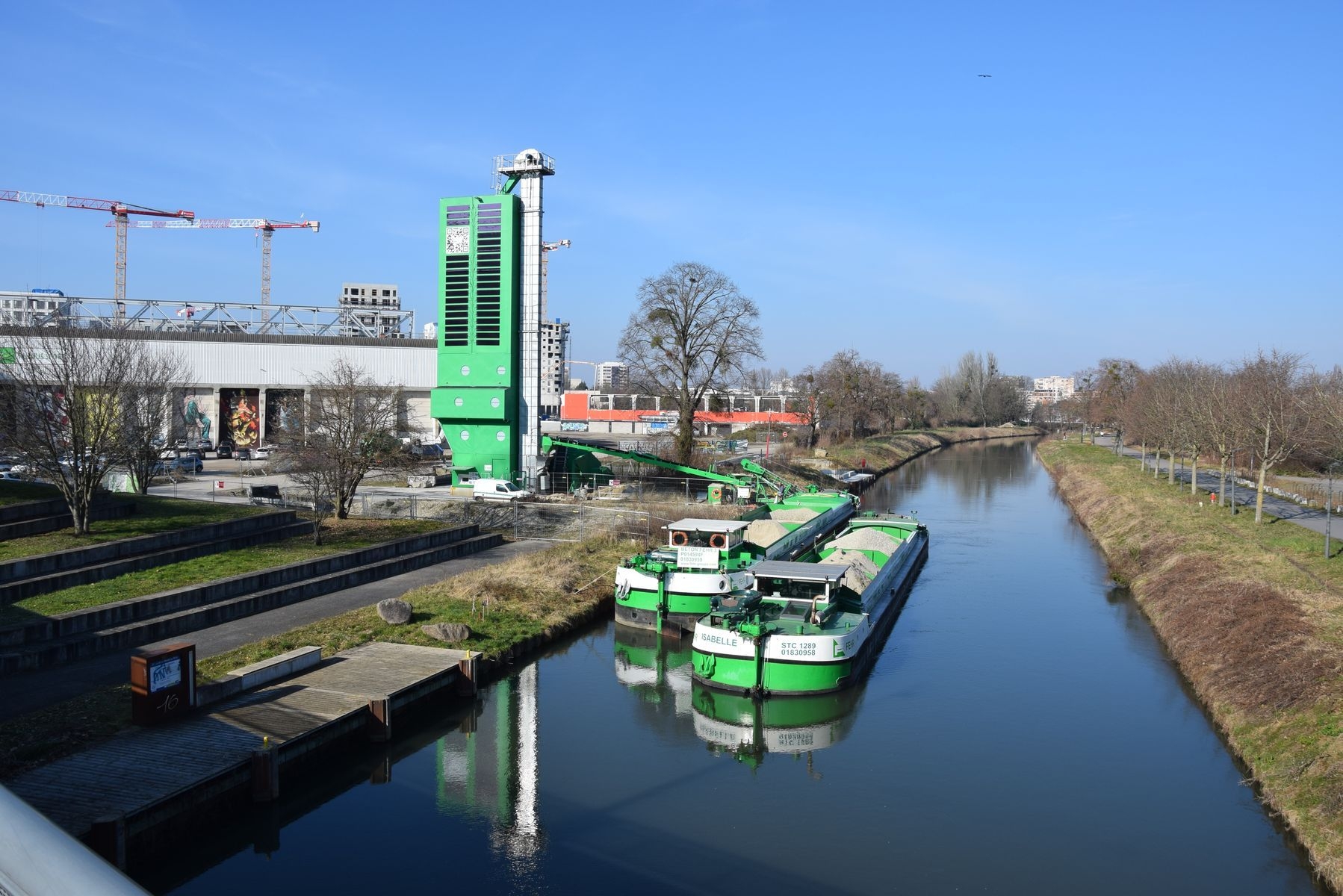
Anticipating for better durability
We do not wait for future standards to act — on-site, all our achievements are already RE2020 certifiable and meet the strictest environmental requirements.
We have contained our greenhouse gas emissions for nearly 60 years by choosing from the outset to favor short supply chains, transport by waterway, and locally produced materials. By using low-environmental-impact concrete and low-carbon raw materials today, Fehr Group supports its efforts in reducing its energy needs and affirms its direction: to be at the forefront of the overall CO2 reduction across the construction sector.
Manage to protect
By using non-polluting products, relying on the direct supply of raw materials, and recycling our waste, we limit our energy consumption: these three axes form the basis of our product management approach.
Moreover, our strategy of siting facilities around major economic hubs offers a local response to client projects, thus further reducing the impact of transport.
The elements are delivered without packaging, and the containers are consigned. Our Précoffré® solution also allows for the advance delivery of containers on-site: this can be scheduled outside of peak traffic times and highway congestions on the eve of weekends, thus contributing to the decongestion of traffic routes.
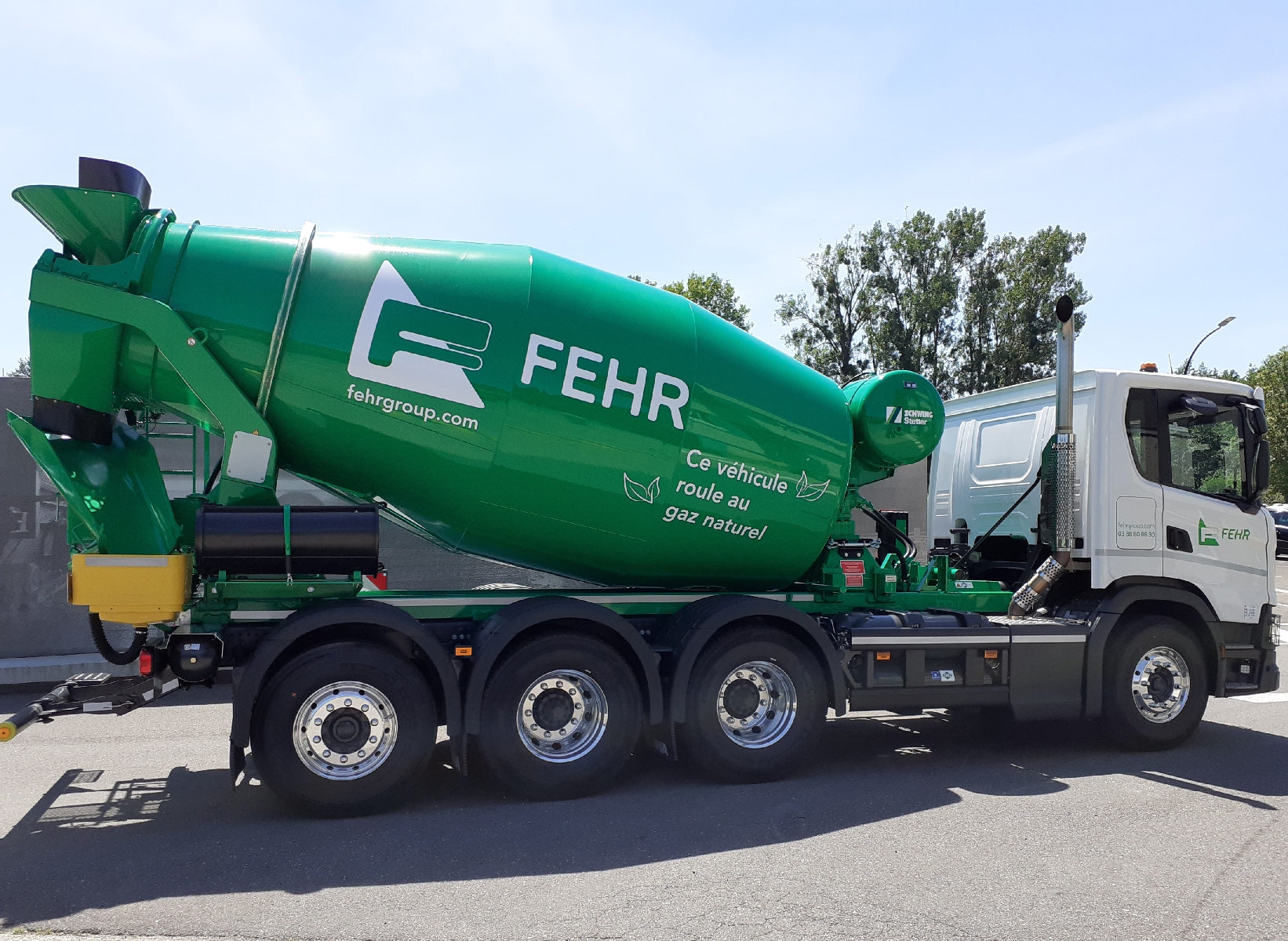
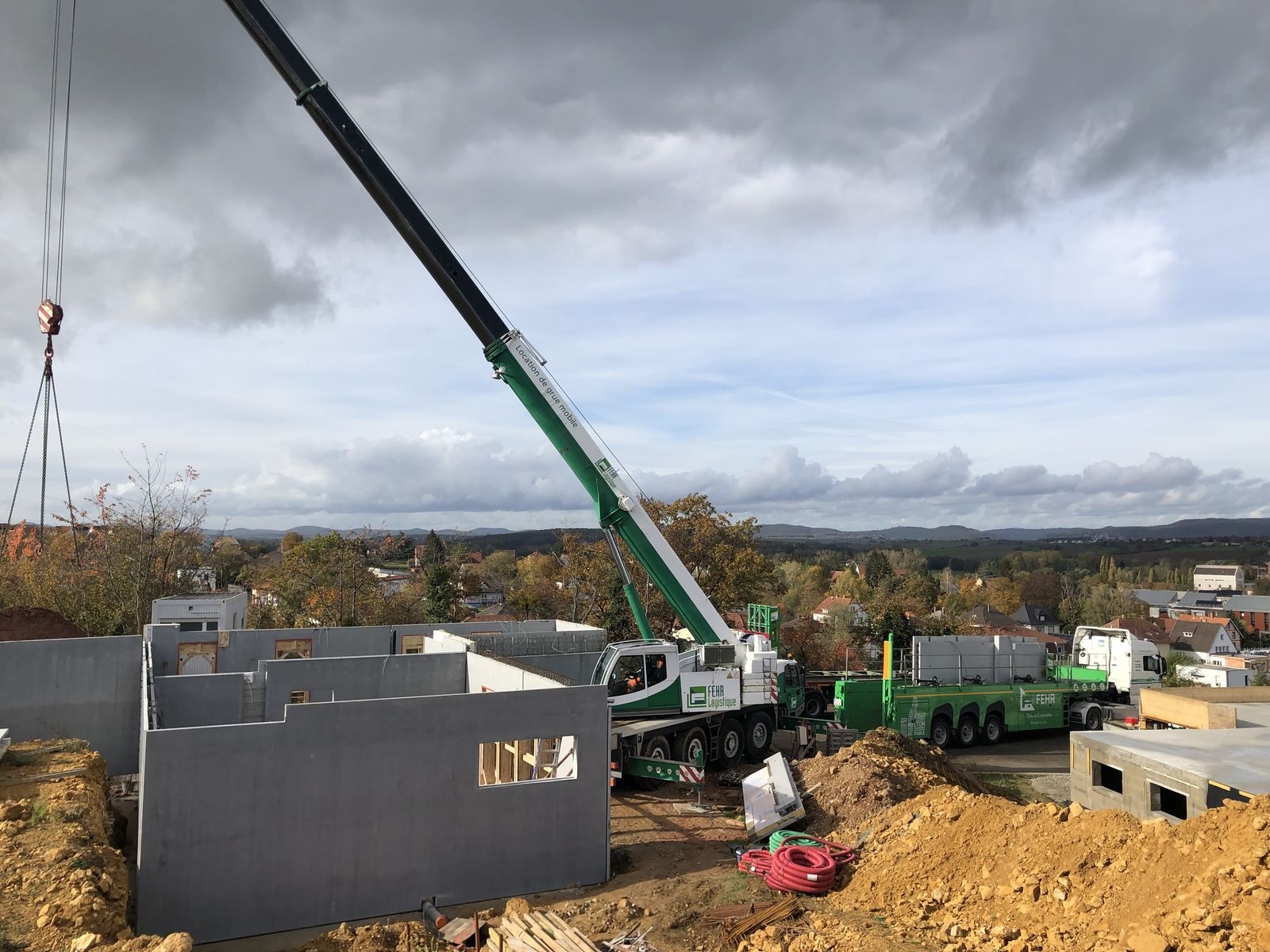
Finally, our products require no formwork panels or release agents on-site. Construction times are shortened, and nuisances related to construction sites are reduced: less consumables, less noise, and less dust for your agents and our employees.
Moreover, our strategy of siting facilities around major economic hubs offers a local response to client projects, thus further reducing the impact of transport.
By aiming for an additional 30% reduction in our carbon footprint by 2020-2030, continuously reducing our waste volumes, and offering low-carbon cement formulations with recycled aggregates and bio-based insulators today, we continue our original commitment: to reconcile the sustainability of activities with improved environmental performance.
Life is too precious to be sacrificed on the altar of competitiveness — and it is out of the question to contribute to uncontrolled pressure on natural resources. Making environmental risk management the core of our priorities: a goal we are proud to achieve. Starting now.
FEHR Group is a member of the French Passive Construction Federation.
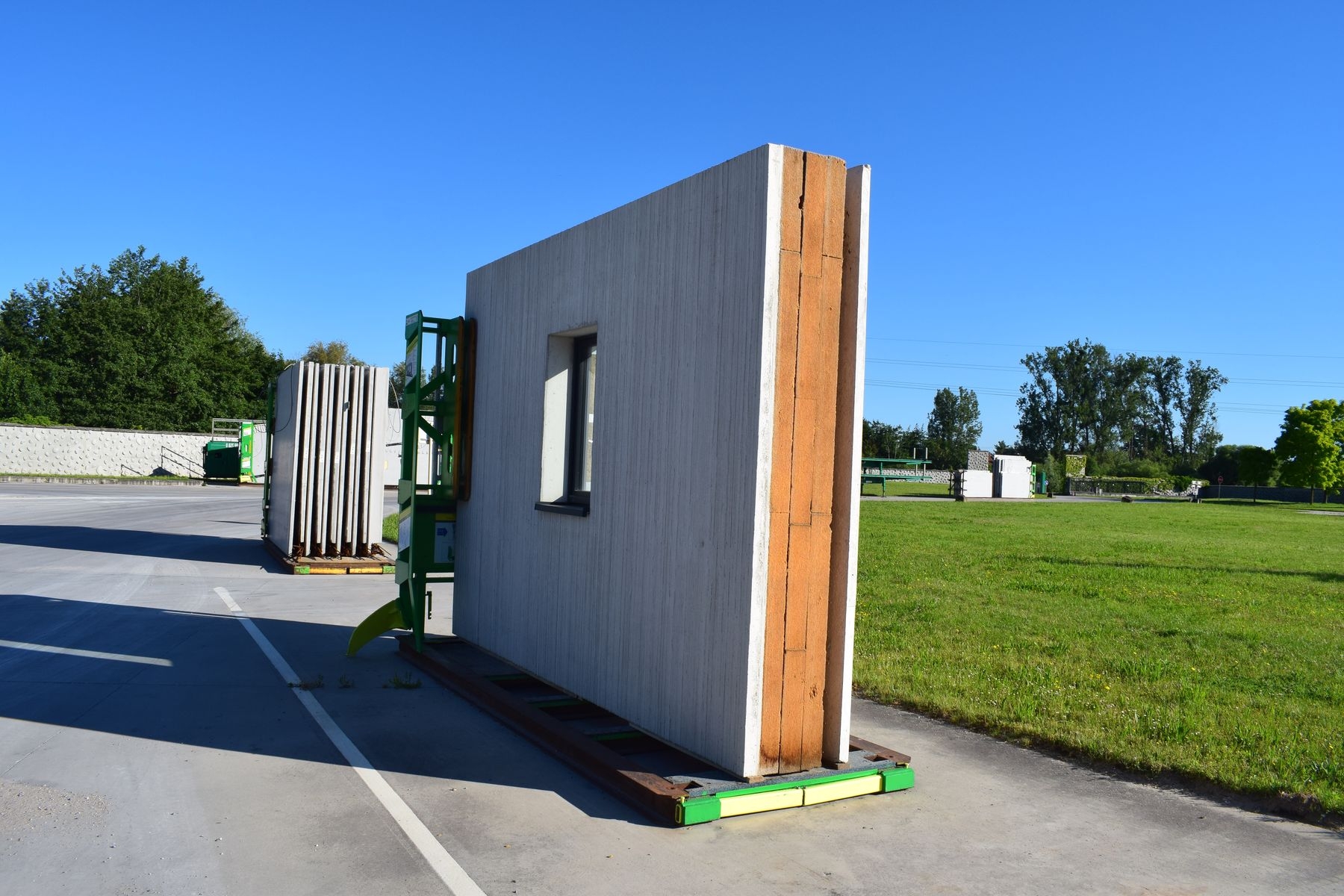
Committed together for sustainable construction
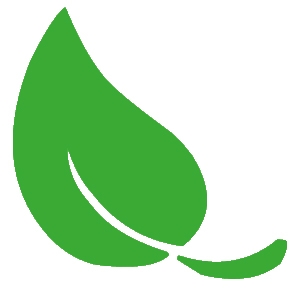
An environmental approach at all our production sites.
FEHR Group places sustainable construction at the heart of its strategy: use of recycled aggregates, recycling of concrete, waste reduction, systematic preference for low-carbon materials.
Our ready-mix concrete and precast element production sites are ideally located near quarries to promote short supply routes and local suppliers, and close to major roadways, as close to our clients' construction sites as possible.
Preserving resources Promoting the circular economy. All our production sites are ISO 14001 certified and meet the requirements for environmental management.
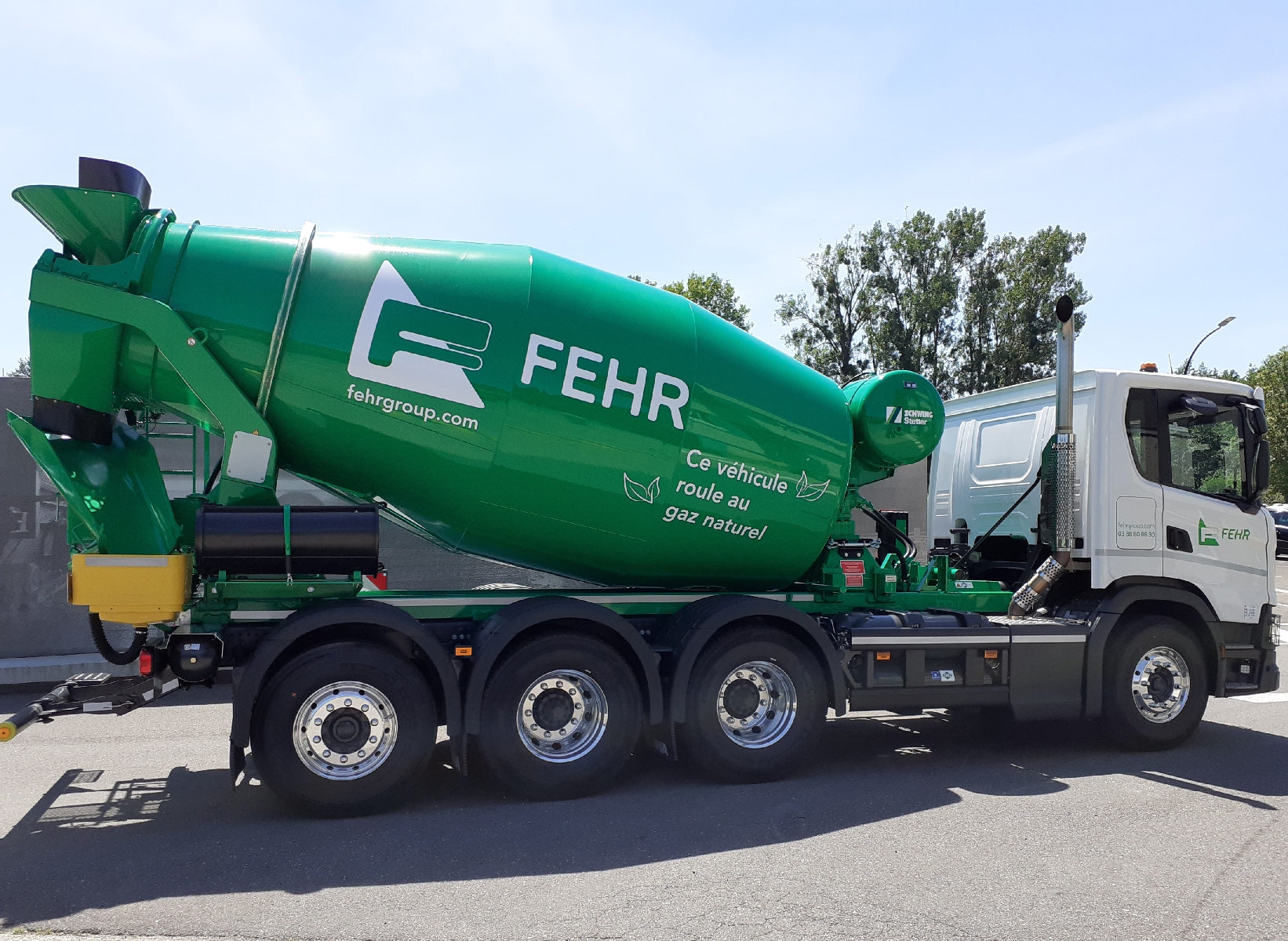
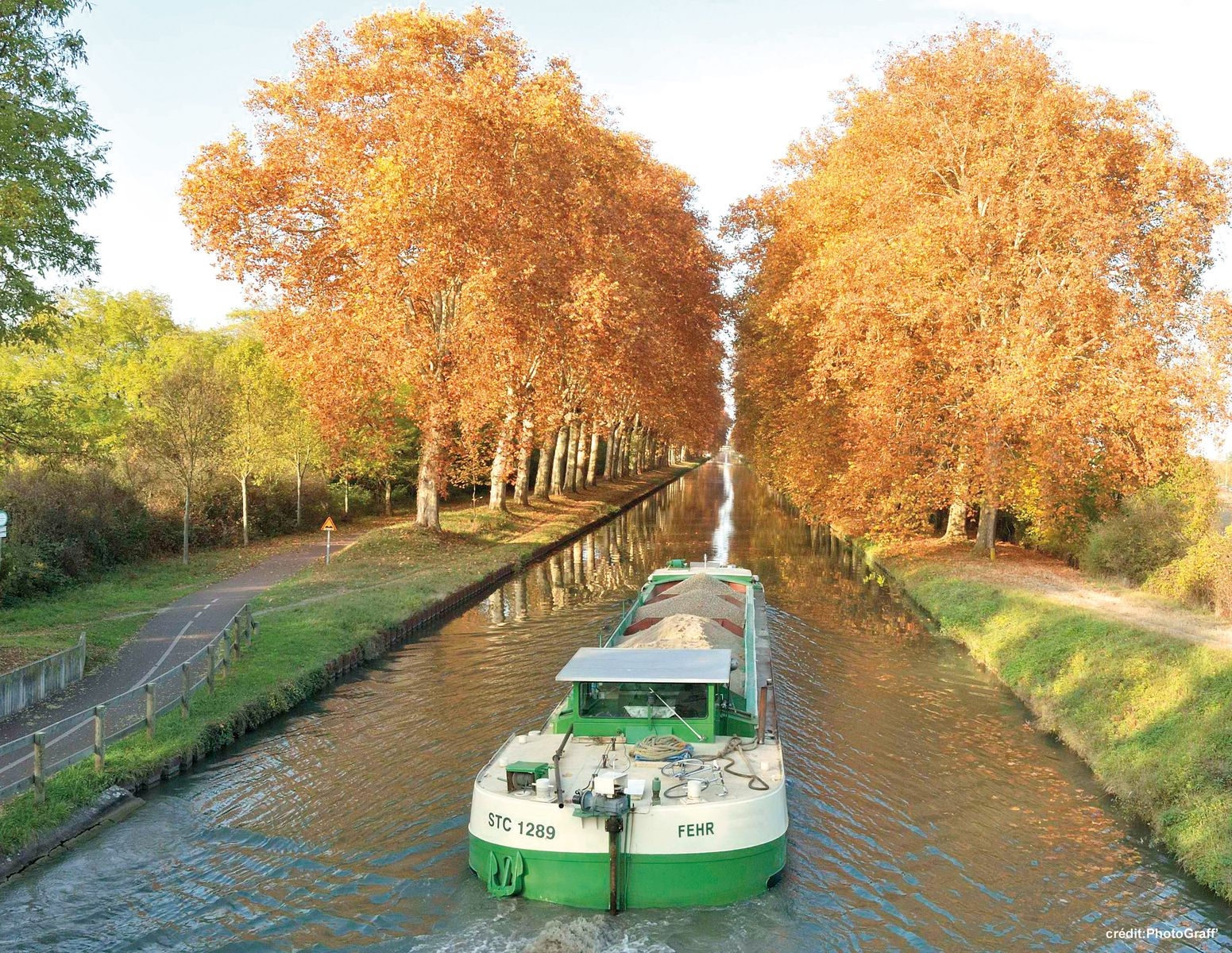
Eco-responsible logistics in all our activities Ready-mix concrete, Précoffré®, Prédalle, or FClad® cladding panel
Our Précoffré® solution is delivered using self-unloading trailers allowing advance delivery of containers on-site: this can be scheduled outside peak traffic times during the day and freeway congestions on the eve of weekends, thus contributing to the decongestion of traffic routes.
Transport by gas-powered truck allows a 20% reduction in CO2 emissions. Alternative transports, such as rail transport, can also be considered, depending on the importance and delivery deadline of the project.
In Alsace (67), to supply some of our plants with raw materials, two barges transport 240 tons of aggregates by waterway each day: 1 barge saves 8 trucks per day, resulting in a 68% CO2 saving on transport.
Our FDriver app (dematerialized delivery slip) also contributes to our environmental approach by eliminating 100,000 paper delivery slips per year and the absence of vehicles charged with their delivery for administrative processing.
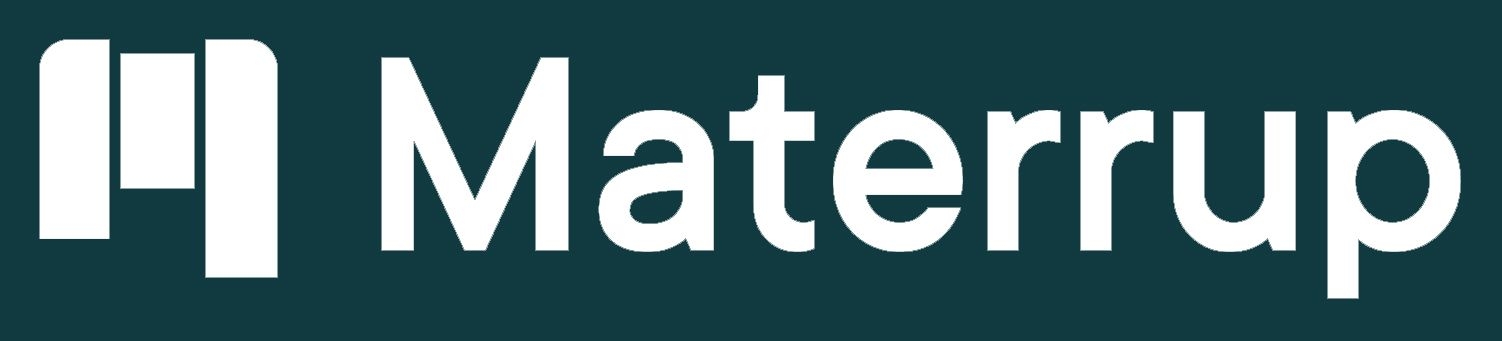
Nos solutions bas carbone avec Materrup
Éléments préfabriqués
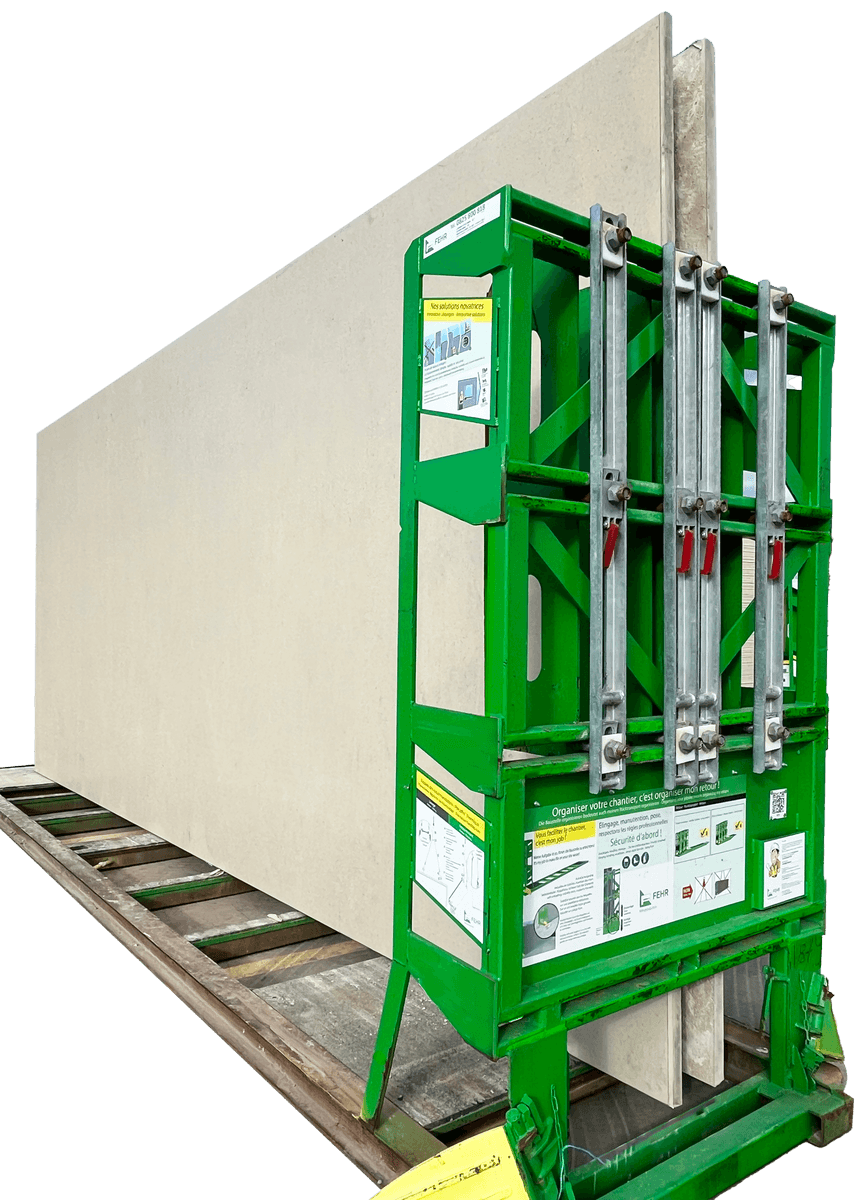
Précoffré® Classique
22,2
kg éq. CO2/m2 ciment Materrup
40,2
kg éq. CO2/m2 ciment CEM I
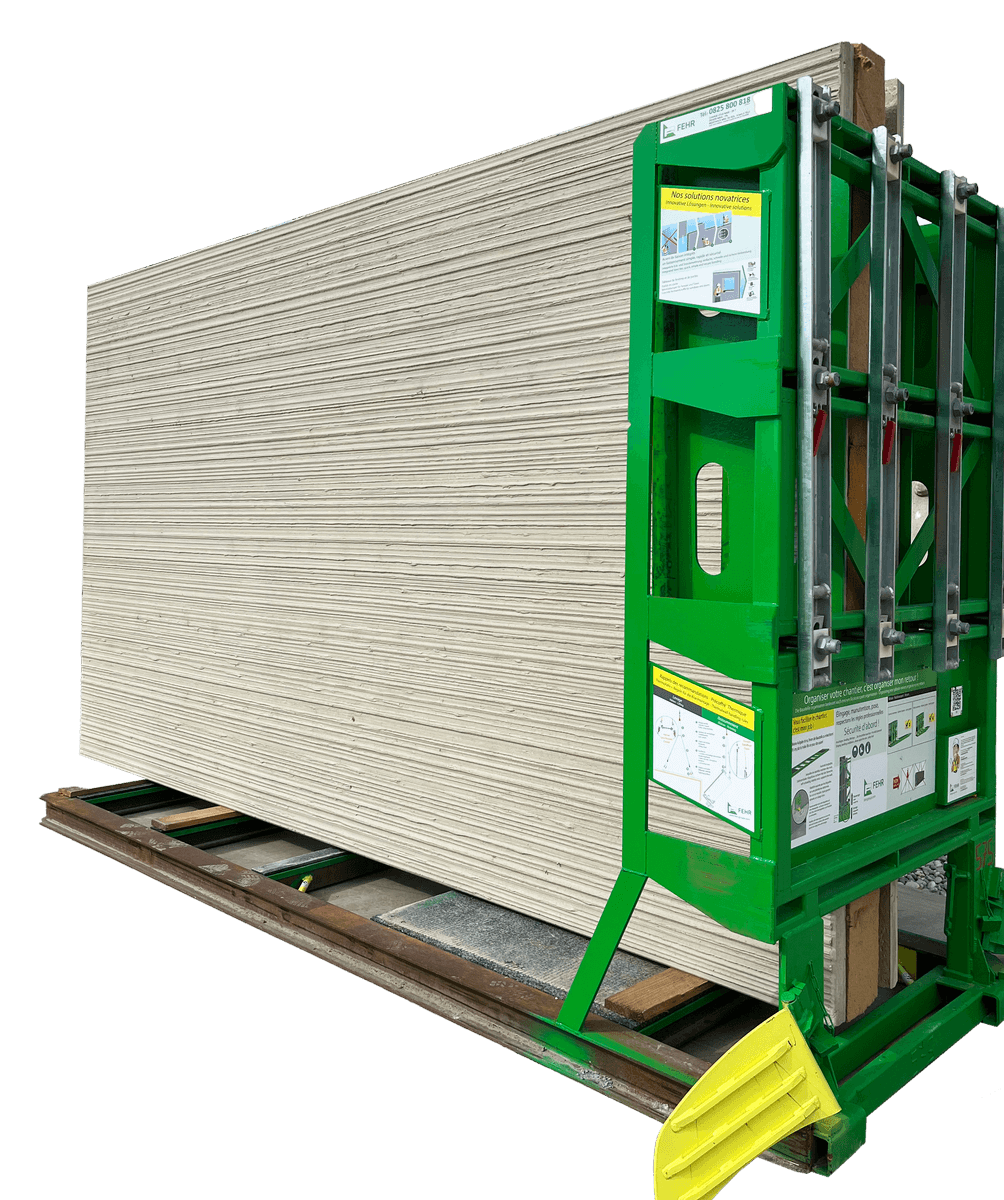
Précoffré® Thermique
40,4
kg éq. CO2/m2 ciment Materrup
71,2
kg éq. CO2/m2 ciment CEM I
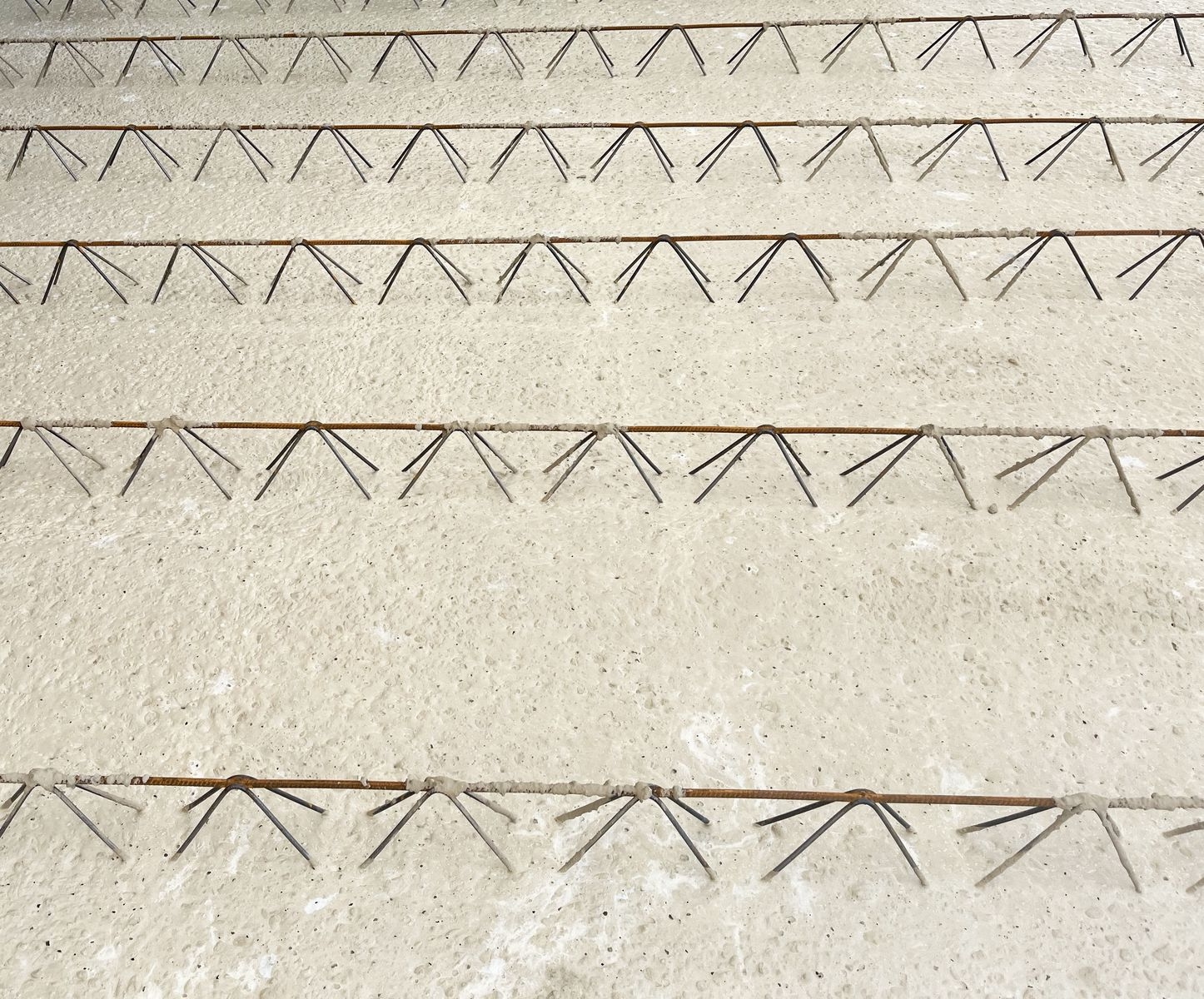
Prédalle
12,3
kg éq. CO2/m2 ciment Materrup
24
kg éq. CO2/m2 ciment CEM I
Le Béton prêt à l’emploi
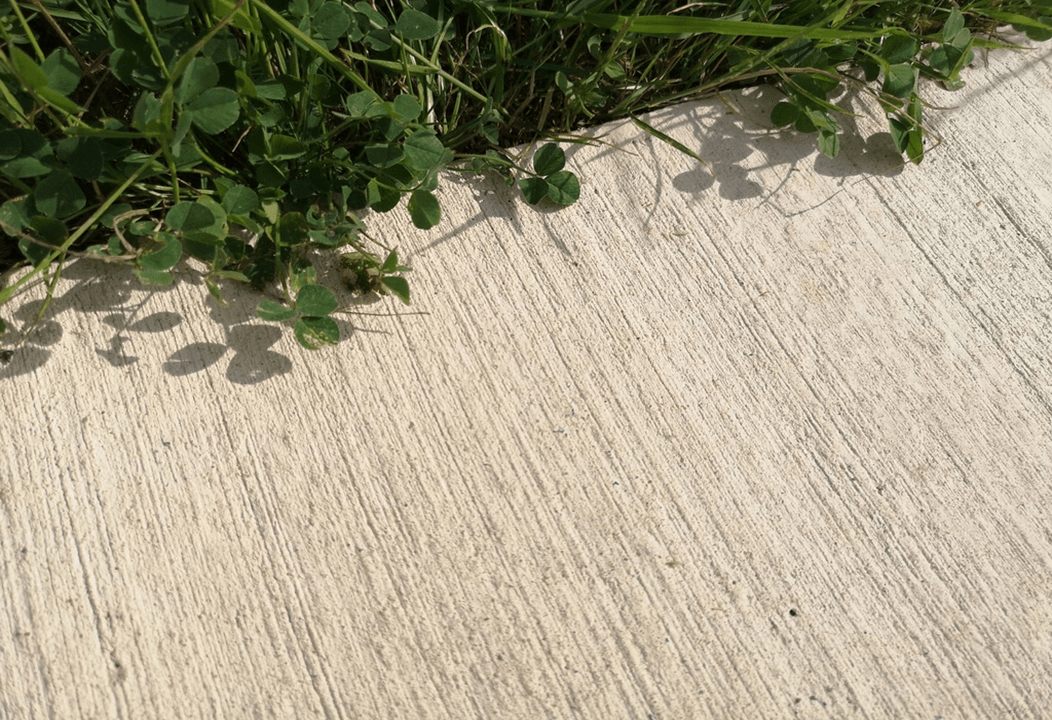
Pour des bétons de dallage, fondation, béton drainant. Mais également des bétons décoratifs (terrazzo, désactivé, bouchardé, balayé)
120
kg éq. CO2/m3 ciment Materrup
262
kg éq. CO2/m3 ciment CEM I
Vers la neutralité carbone
Objectif : -35%
Objectif : -100%
- Livraison par camion gaz : -20% d’émissions de CO2
- Formulation en ciment CEMIII -30% d’émissions de CO2 par rapport à un béton en CEMII
- Précoffré® TH Green : Rmur = jusqu’à 8,65 m2.K/W
- Formulation béton - Précoffré® :
- Bas Carbone -43% / Super Bas Carbone -51%
- Précoffré®, départ usine, sans remplissage :
- Bas Carbone -34% / Super Bas Carbone -40%
- 100% granulats recyclés
- Carbonatation des granulats recyclés
- Captage CO2